Enhanced Sealing Performance
Gaskets serve as seals that prevent leaks and protect machinery from external contaminants. Injection molded gaskets offer enhanced sealing performance due to their ability to be precisely manufactured to fit unique shapes and sizes. This customization minimizes the risk of leaks and ensures a secure seal, even in applications where tight tolerances are crucial, such as in automotive engines or industrial pipelines.
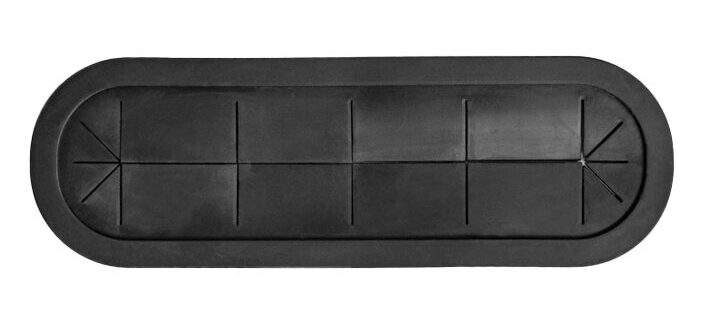
Customized Material Properties
One of the standout advantages of injection molded gaskets and grommets is the ability to tailor material properties to specific requirements. Engineers can choose from a wide range of plastic materials, each with unique attributes like heat resistance, chemical resistance, or electrical insulation. This customization allows for the selection of materials that best match the demands of the intended application, ultimately optimizing performance and durability.
Cost-Effective Production
Injection molding is a highly efficient and cost-effective production method. It enables the mass production of intricate gasket and grommet designs with minimal waste. The ability to create complex shapes in a single manufacturing step reduces labor costs, tooling expenses, and overall production time. This makes injection molded gaskets and grommets a viable solution for industries that demand high volumes of components.
Noise & Vibration Dampening
Injection molded gaskets and grommets often exhibit inherent noise and vibration dampening qualities due to the properties of plastic materials. This is particularly advantageous in applications where noise reduction is essential, such as in automotive interiors, household appliances, or electronic devices.
Environmental Resistance
Plastic materials used in injection molding are known for their resistance to environmental factors, such as moisture, chemicals, and UV radiation. This property ensures the longevity of gaskets and grommets in various environments, including outdoor settings and industries with high exposure to corrosive substances.
Seamless Integration of Features
The flexibility of injection molding enables the integration of additional features directly into the gasket or grommet design. For instance, gaskets can be molded with built-in grooves, channels, or barriers to enhance sealing efficiency. Grommets can include cable management features, such as routing channels or strain relief points. This integration simplifies assembly processes and optimizes component functionality.
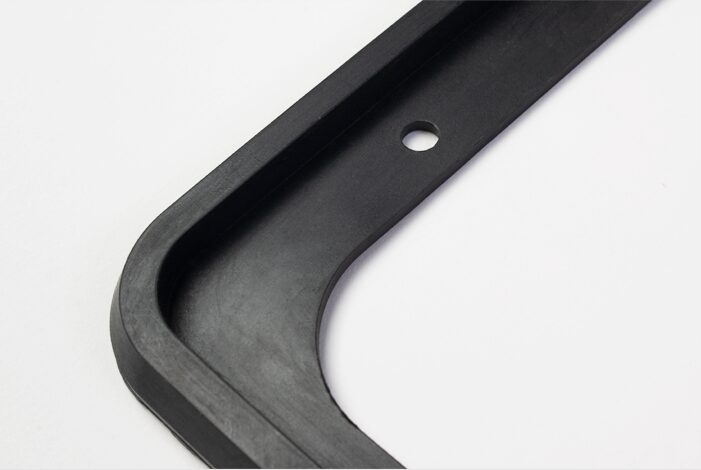
Injection molded gaskets and grommets are leading the way in modern engineering solutions, offering a plethora of advantages that cater to diverse industrial needs. From enhanced sealing performance and customized material properties to cost-effective production and resistance to environmental factors, these components are reshaping the landscape of industries that rely on precision, efficiency, and longevity. As technology continues to advance, we can anticipate further refinements in injection molded techniques and materials, continually elevating the benefits these components bring to various applications.